To celebrate its 1,150th anniversary, the Monnaie de Paris launched the “Excellence à la française” collection in 2014, in homage to major French institutions and houses (the Louvre, Dior, etc.). A few weeks before the reopening of Notre-Dame de Paris, the Parisian establishment is today presenting a new collection of seven pieces bearing the image of the cathedral. The most prestigious, the one kilo gold coin, takes the shape of a Gothic window. The facade of the cathedral and a rose window decorate its obverse (the obverse side), while the reconstructed nave and its framework unfold on the reverse of the coin. From engraving to striking, including the delicate enamelling of the rosette, follow the journey of creating this exceptional piece in the workshops of the Monnaie de Paris.
The last monetary workshop in France
Created in 864 under Charles II, the Paris Mint has been installed along the Seine, Quai de Conti in the 6th arrondissement of Paris, since 1775. It is the last remaining workshop of the old French monetary network. If its Pessac site in Gironde mints current currencies, the historic site of the Quai de Conti is dedicated to the manufacture of collector's coins.
The seven coins from the collection dedicated to Notre-Dame de Paris © Monnaie de Paris
Three hundred and fifty craftsmen work there, spread across around fifteen workshops. Among them, the engraving workshop where the models and preparatory pieces for each new collection are designed, and the coiners' workshop, where the coins are minted. The most prestigious, such as medals or “kilo gold” coins, are then sent to the enamelling workshop.
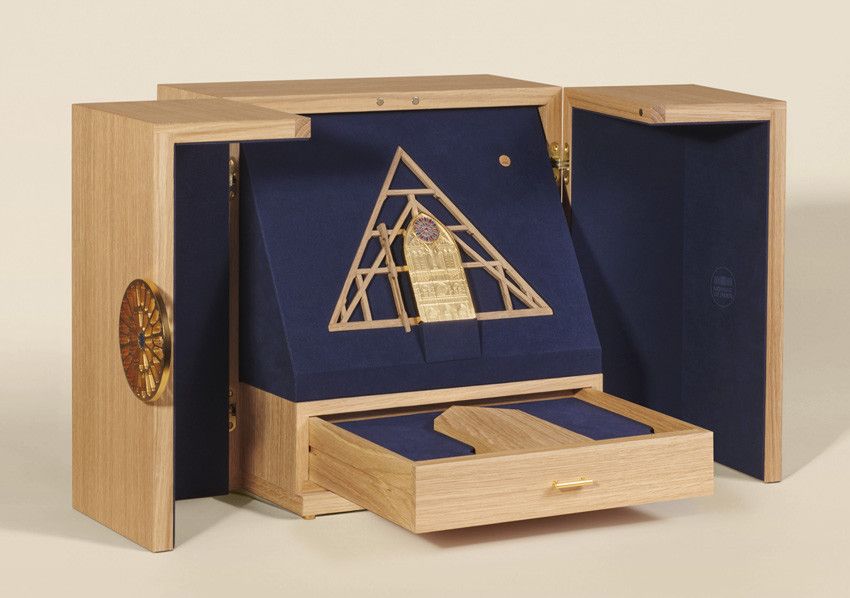
The one kilo gold coin is presented in a wooden box, paying homage to the framework of Notre-Dame de Paris © Monnaie de Paris
The “French Excellence” collection
Since 2014, Monnaie de Paris has produced a collection of excellence each year, in association with an institution or a prestigious house. It includes coins of various metals – gold, silver, copper – and a gold coin weighing one, or sometimes two kilos, sold to collectors. This year, Notre-Dame de Paris Cathedral is in the spotlight for its reopening scheduled for December 8. To create the models, the artisans of the Monnaie de Paris and those of Notre-Dame consulted at length.
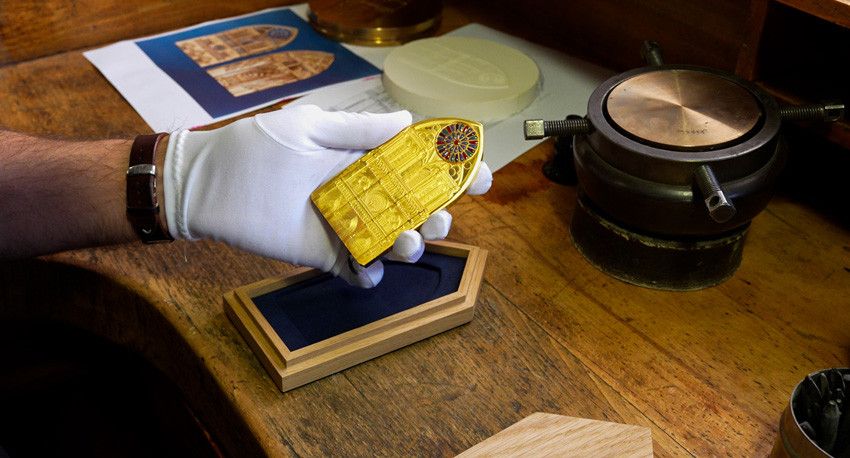
The one kilo gold coin, the most exceptional coin in the Notre-Dame collection © Guillaume de Roquemaurel
In the engraving workshop
The creation phase begins in the engraving workshop. Nine engravers work there, all trained in prestigious schools such as the Boulle school, the Estienne school, or the Beaux-Arts. It takes around ten years for an engraver from the Monnaie de Paris to master the entire range of knowledge of the profession: drawing, modeling, engraving, hollow and reverse tooling in steel, computer software, and production tools with digital controls.
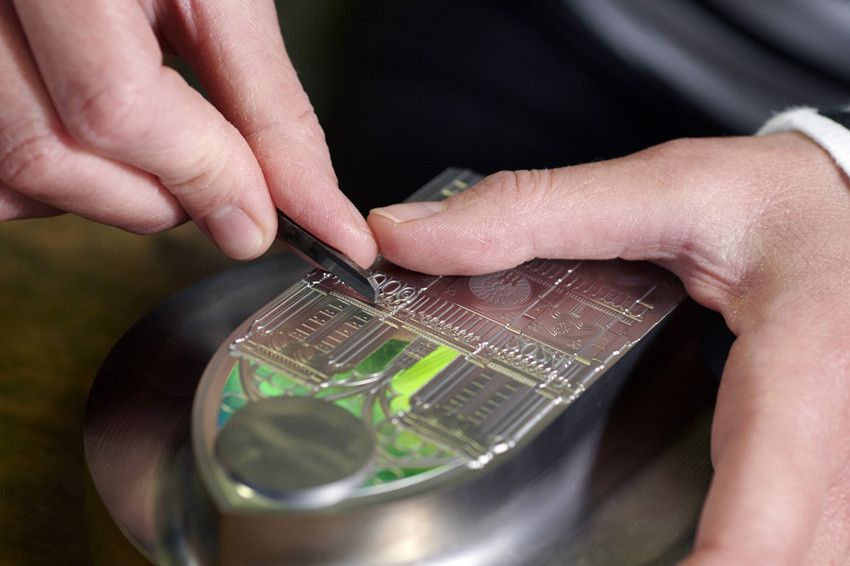
The matrix being engraved © Monnaie de Paris
The engraver first offers a model in the form of a drawing. Once validated, this is used to make a first volume sketch, using plastiline, a modeling clay. The latter is then used to create a negative plaster, which will be reworked. When the model is complete, a positive plaster is cast from the negative. “A model is successful when there is a match between the volume and the design. The difficulty of our job is having to create shortcuts to give the illusion of depth” underlines Yves Sampo, master engraver-medalist responsible for the workshop.

The engraved matrix which will be used to mint the coins © Monnaie de Paris
A currency with an original shape
For the Notre-Dame de Paris collection, the choice of the shape to give to the “kilo gold” piece was made in consultation with the carpenters from the cathedral construction site, whom the engravers met. They opted for a form of mullion window, a window typical of Gothic architecture, allowing the facade of Notre-Dame and its colored rose window to be displayed on the obverse, and the interior of the cathedral on the other side. and the framework rebuilt.
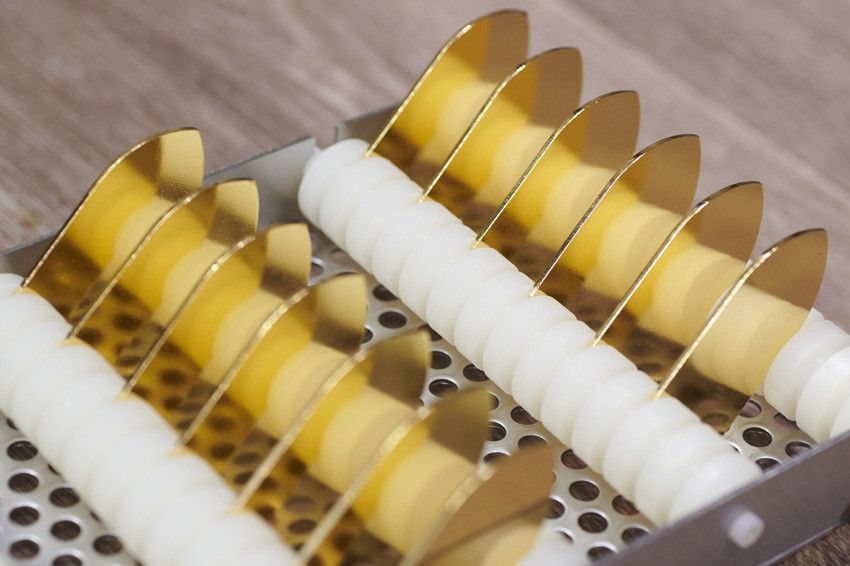
The sides, laser cut and polished, before being minted © Monnaie de Paris
When the shape of the engraving is ready, the matrix is sent to the workshop where the machines used for striking are assembled. The metal, laser cut and polished in the form of a sidewall, is placed in a ferrule and struck. It's a very detailed job where you have to take your time so that everything is perfect. Then, to color the cathedral rose window, the “kilo gold” gold pieces are sent to the enamelling workshop.
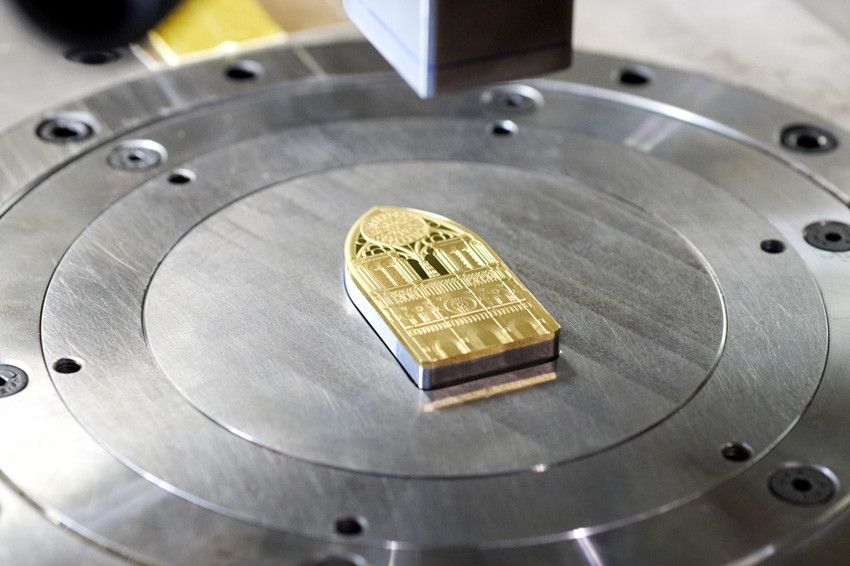
The side is placed in a shell before being struck by a machine exerting a force of around seven hundred tonnes © Monnaie de Paris
Obtain the most transparent enamel possible
Applying the enamel, a crystal powder colored with metal oxides, represented a challenge for the workshop. The objective was to find a balanced “bulge”, and to maintain transparency of the colors so that the chiseled patterns would appear. To obtain the most transparent enamel possible, the colors are ground, refined as much as possible, then washed, that is to say cleaned with demineralized water until the rinsing water is completely transparent.
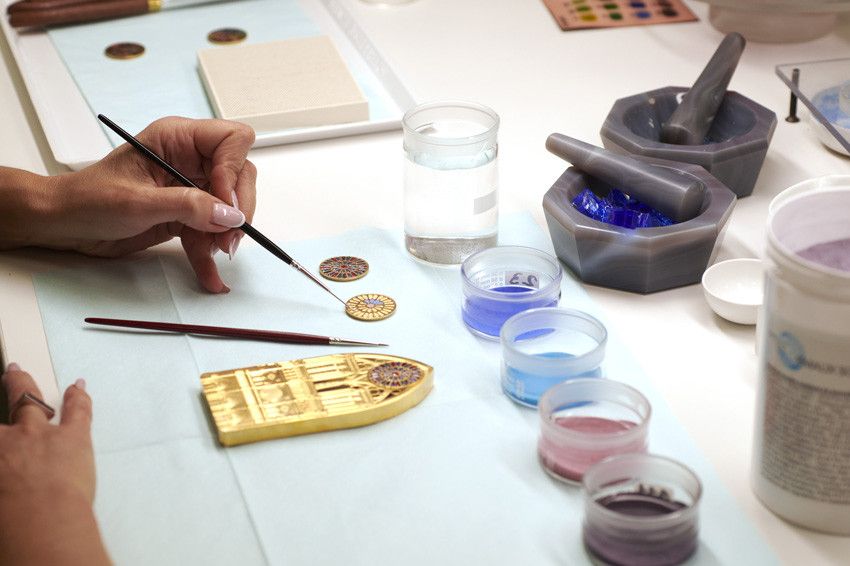
Several skills were called upon for the creation of this piece, for example enamelling for the coloring of the rose window © Monnaie de Paris
The enamel is then placed wet on the piece and dries several hours before being put in the oven, the most complex part of the work. Everything is done in the oven, the enamel is capricious and the oven always has the last word; the important thing is to obtain a rosette with transparent colors and a perfectly homogeneous “bulge” over the entire piece. The oven is heated between 750 and 900 degrees, the cooking time is very quick – between 3 and 4 minutes – and the cooking is done under the eye of the enameler.
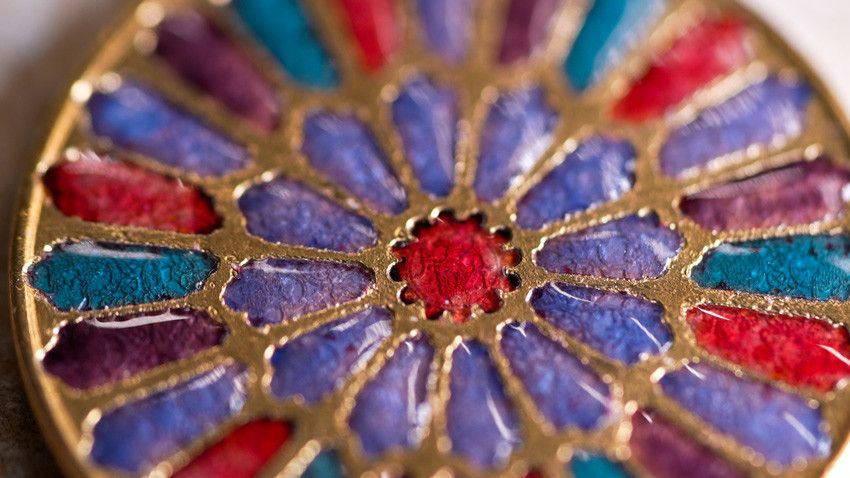
The enameled rosette, revealing the engraved motifs through transparency © Monnaie de Paris
“Notre-Dame represents for us a strong symbol, a culmination of renovation and renewal after this tragedy. We put all our hearts into it. » summarizes Catherine Vérin, enameler jeweler. The result bears witness to this: the piece is luminous, fine, precise, and pays perfect homage to the new restored cathedral.
Today, centuries-old crafts are becoming rare professions !
“Connaissance des Arts” has been defending these often little-known professions for ten years, at the crossroads of hand and mindarts and crafts and creation.
Today it becomes necessary to mobilize so that craftsmen are recognized as true creators and that are implemented the means necessary for the transmission and perpetuation of their know-how.