(Toronto) Metro is heading into 2025 with a renewed capacity for business growth after reaching the final stage of its seven-year, nearly $1 billion supply chain transformation. It added new automation technology to its warehouses in Quebec and Ontario.
Posted at 4:53 p.m.
Rosa Saba
The Canadian Press
In an increasingly competitive industry, Metro needed to evolve its supply chain so that it could remain adaptable and continue to grow its business.
The company’s distribution network had reached its limit in terms of inventory, delivery volume and assortment, forcing it to “struggle to serve” its stores, according to Yanick Blanchet, vice president of the chain Metro supply chain.
PHOTO CHRISTOPHER KATSAROV, THE CANADIAN PRESS
Yanick Blanchet, vice-president of supply chain at Metro.
The completion of Metro’s supply chain overhaul, which began in 2017, was marked this year by the opening of the final phase of its new automated fresh produce distribution center in Etobicoke, Greater Toronto, Ontario. This follows Metro opening an automated warehouse for frozen goods also in Etobicoke in 2022. In Quebec, the company opened a new automated fresh and frozen goods center in Terrebonne last year and expanded its fresh produce center in Laval.
“This is a major investment that will allow us to support growth over the coming years,” said Mr. Blanchet during an interview at the new fresh produce distribution center in Etobicoke.
How does it work?
Thanks to automation, Metro’s distribution centers are able to fit a significantly higher volume of products into a similar square footprint, Mario Duran, director of logistics and engineering, explains during a tour.
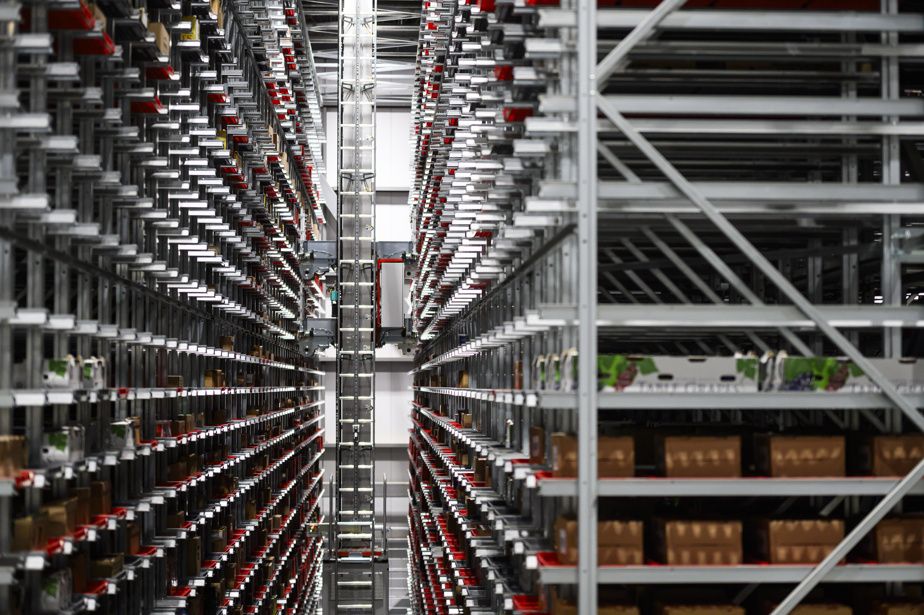
PHOTO CHRISTOPHER KATSAROV, THE CANADIAN PRESS
Storage can go much higher with automation. Parts of the distribution center are 100 feet high.
Using automation means storage can go much higher – parts of Etobicoke’s new produce center are 100 feet high, while the old warehouse’s ceilings were only 30 feet high. The center’s total footprint is nearly 567,000 square feet, shipping 1.1 million cases per week.
The newly completed center houses a mix of automated, semi-automated and conventional operations that bring products such as meat, flowers and dairy to Metro’s 277 Metro and Food Basics stores in Ontario.
The first phase of the center, built next to an existing warehouse, was commissioned in January 2021. Once the transition to this building was completed, the neighboring building was demolished to make way for the second phase, which was commissioned last June.
Certain products, such as raw meat, cannot be processed by the automated system for safety reasons, emphasizes Mr. Blanchet. Others do not operate in the fully automated section due to the packaging they come in, although Metro is working with suppliers to make more products eligible for automation in the future.
“We want to get the most out of (our investment),” says Mr. Blanchet.
In semi-automated spaces, robotic cranes transfer products from the top of the shelves to the base of the shelves, where they are picked up by workers operating electric pallet jacks.
In the fully automated part, a multi-level city of conveyor belts and machines hums, while crates of grapes, iced tea, avocados and orange juice are moved from one location to another. From a command center on the ground floor, workers monitor the operation.
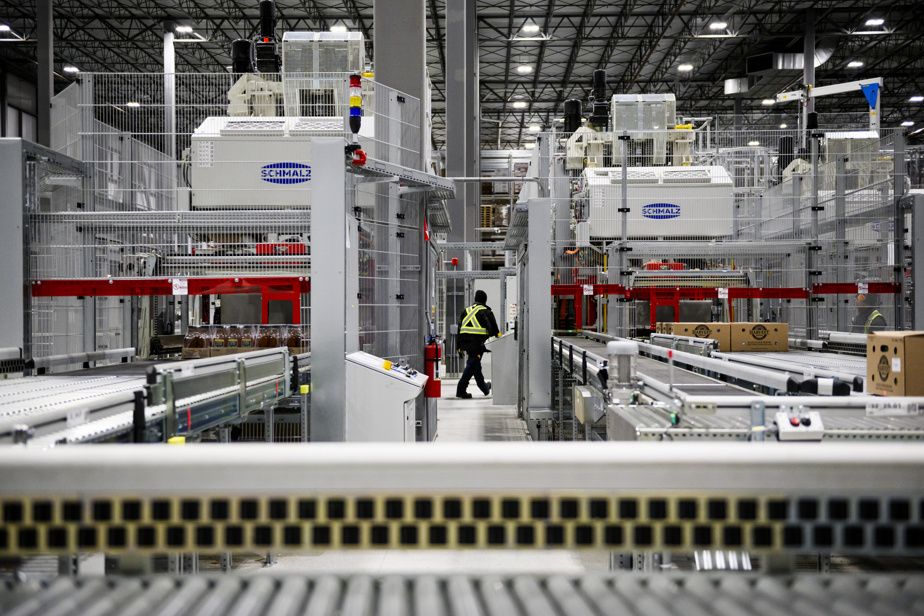
PHOTO CHRISTOPHER KATSAROV, THE CANADIAN PRESS
Conveyor belts are used to move goods around the distribution center.
Here, pallets from suppliers are unloaded and crates of product are sorted and stacked for short-term storage.
Rows of 80-foot-tall metal lockers make up the short-term storage area. The lockers are navigated by 28 automated cranes, traveling at up to 30 km/h to place the boxes in the lockers and remove them.
The cases are reloaded onto pallets in seemingly random order to form a pile that is then wrapped in plastic, ready to ship to grocery stores.
The system, designed by the German company Witron, takes into account information about incoming shipments, such as dimensions, weight and fragility of boxes, as well as store orders, and generates a series of pallet models, playing playing a theoretical game of Tetris before building what Mr. Blanchet calls “the perfect palette” in real life. The 14 machines that build the pallets can each handle around 500 cases per hour.
More retailers are investing in automating their warehouses, observes retail analyst Bruce Winder. The technology helps reduce costs, speed up operations and improve accuracy, he says.
Competitors Loblaw and Empire have also added automation to their supply chains in recent years.
“It’s kind of an interesting evolution in grocery in terms of how they’re using centralized distribution and automation,” Winder says.
Room to grow
The new centers require different skills and training than a conventional warehouse, Blanchet points out – they are more maintenance-oriented, but they also offer more enjoyable jobs, many physically demanding tasks like moving boxes. out of a freezer being largely eliminated from the equation.
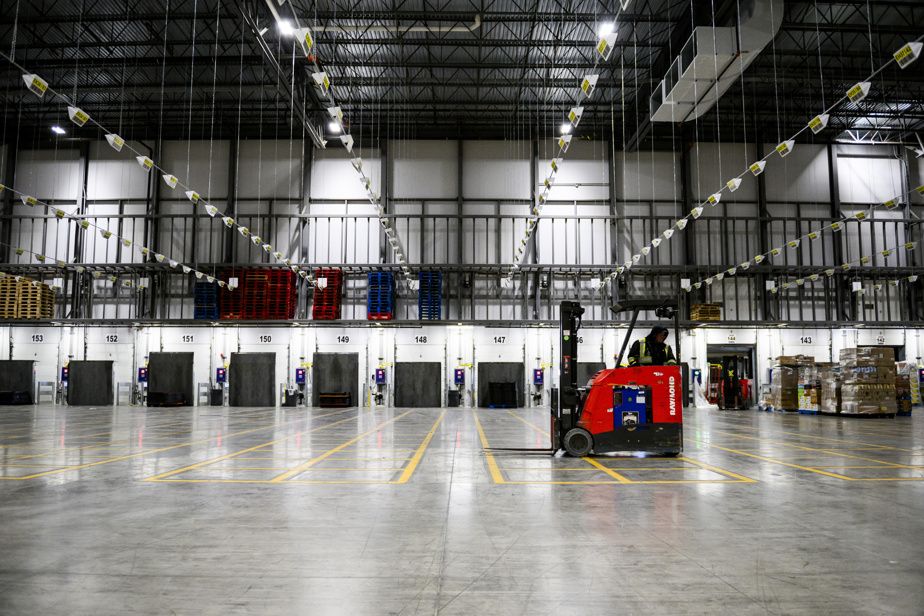
PHOTO CHRISTOPHER KATSAROV, THE CANADIAN PRESS
A center employee travels aboard a forklift.
“We need less manpower… but we need more expertise,” specifies Mr. Blanchet, while adding that Metro intended to make the change without layoffs.
Although work on the project began before the COVID-19 pandemic, the pandemic and other supply chain disruptions have shown how important it is to have a resilient supply chain with plans integrated emergency services, according to Mr. Blanchet.
Over time, the new distribution centers will support additional growth, reduce the impact of labor shortages, prevent product damage, improve order accuracy and increase efficiency, making deliveries fresher , specifies Mr. Blanchet.
The changes also allow Metro to increase its assortment by delivering more products from its distribution centers instead of relying on suppliers to deliver directly to stores, he adds.
Winder says this is another increasingly common feature of retail supply chains, and not just in grocery.
“Instead of having the supplier ship all these disparate pallets that are inefficient, they send pallets that are…picked correctly and much more efficient, transportation-wise,” he explains.
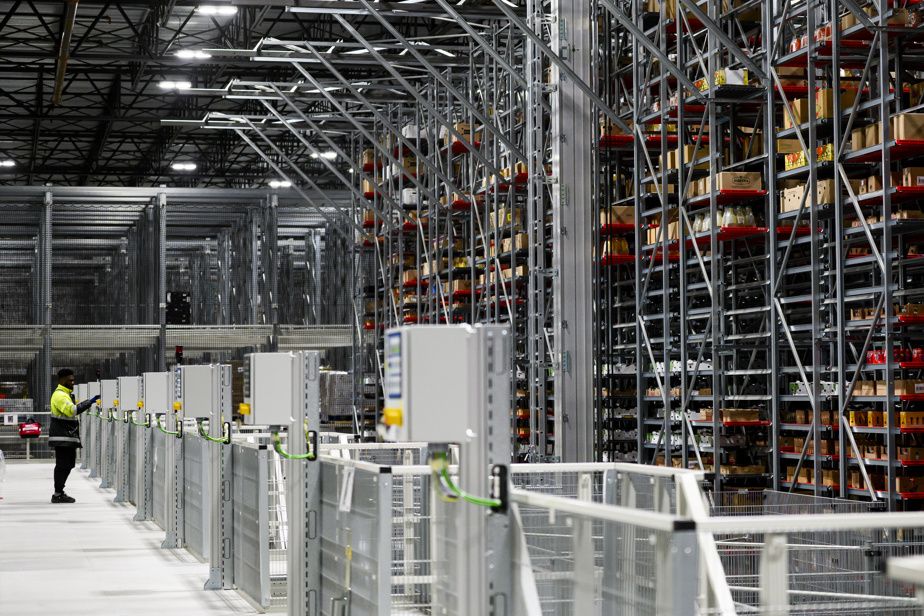
PHOTO CHRISTOPHER KATSAROV, THE CANADIAN PRESS
This method also reduces waste because each store gets exactly what it needs, according to Winder.
“There are all kinds of benefits, and a lot of other retailers have been using this model for decades. »
The new network has plenty of room for growth, Blanchet concludes, and automation paves the way for continuous improvement and new opportunities.
“When you make a major investment like this, you want to make sure it’s long term. »