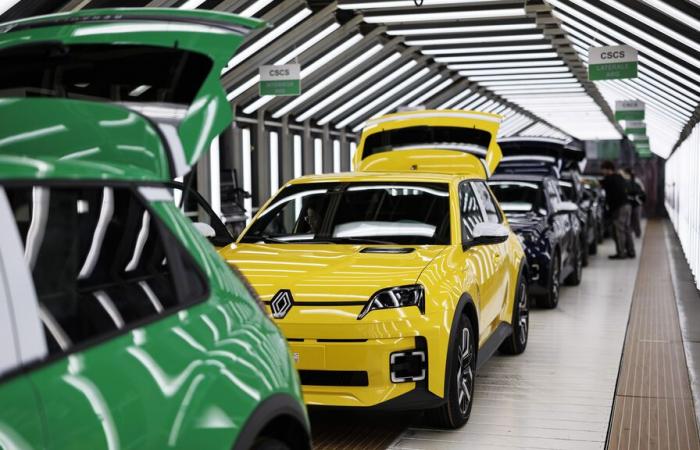
Renault is taking a gamble by choosing to revive an industrial site that is losing momentum. Far from the 469,510 vehicles produced in 2004 during the heyday of the Scénic, Douai experienced a long journey through the desert from 2019 due to the pandemic and sluggish sales. Production remained low in 2023, with 51,486 examples (mainly Mégane). A change of gear is planned for 2025, with the ambition to manufacture 400,000 vehicles. “When I arrived, there was nothing here, it was empty,” recalls Luca de Meo, general manager of the group since 2020. One of his first decisions was to localize the group's new electrical products in France, by creating a complete ecosystem called “Electricity” and a B2B brand dedicated to design and the industrialization of electric vehicles, Ampere. “I was told I was completely crazy when I made this decision,” continues Luca de Meo.
Industrial compaction and logistics optimization
However, a snap of the finger was not enough to restart the machine. Multiple developments and investments have been made to ensure the competitiveness of the Manufacture. “The transformation began in 2021,” says Pierre-Emmanuel Andrieux, the factory director for four years. First there was the installation of the new assembly line, designed according to the industrial standards of the Renault-Nissan-Mitsubishi Alliance and which now extends over a single floor, and no longer two. Its implementation was concomitant with serious compaction of the industrial site. The latter is today reduced to 118 hectares, including 32 of covered buildings thanks in particular to the sale in 2021 of 144 hectares to AESC Envision. The Sino-Japanese battery manufacturer has erected a gigafactory there, which must begin delivering Renault battery modules for the R5 from March 2025. These will travel by small train the 500 meters which separate their production site from the Renault factory.
“We have also reduced our covered surfaces by 32%,” assures Pierre-Emmanuel Andrieux, who tried to optimize the logistics of the factory to gain efficiency and reduce costs. “We have carried out stock reductions and optimizations of our processes”, with the integration of a logistics platform, made possible thanks to the establishment of a large number of suppliers nearby (Renault claims the presence of 75% of its suppliers within 300 kilometers). “The organization for supplying parts has changed, continues Pierre-Emmanuel Andrieux. If you pick up your parts 50 kilometers from here, you need much less safety stock than if you pick up your parts thousands of miles away! From the moment we reduce our stocks, we need less storage space, which allows us to free up space to integrate processes such as battery assembly. This workshop has been located since 2021 in the same building as the final assembly of the vehicles. Around a hundred people manufacture up to 500 batteries per day, using battery casings manufactured at the Ruitz factory (Pas-de-Calais).
Produce the R5 in less than 10 hours
In line with all these modifications, one goal: “reduce the cost of the industrial system by 50%. We have already reached 30%,” welcomes Pierre-Emmanuel Andrieux, who knows that there is still a long way to go. The director is counting in particular on the improvement of the organization of workstations and a fully connected factory in 2027. But another important step is arriving in the meantime: producing the R5 in less than 10 hours flat, and ultimately aiming for 9 hours ! This task falls to Ampere's new director of industrial operations, Anne-Catherine Brieux. “The objective is to get there by the end of 2025 and then aim for 9 hours to do better and faster than our competitor, who is around 35 hours of production,” explains Thierry Charvet, the industrial and quality director of the Renault group, with implicit reference to Tesla. Way to remind us which competitors Renault compares itself to and which it wishes to beat to the post.
This objective is achievable because “the R5 has genetics in terms of design to be produced in less than 10 hours”, continues Thierry Charvet. The model has around 1000 parts, compared to 1500 on previous models of the group. “And we are aiming for 750 on the future Twingo”, completes Luca de Meo.
At the end of October, the Douai factory was in its fifth week of ramp-up, capable of producing 530 cars per day, including around 300 R5 models. The factory with 2,853 employees hired 450 people, 33% of whom were women, to meet the production needs of the new flagship model of the Losange. If the factory is currently running with a team and a half, the pace should soon accelerate. The Manufacture will produce the white bodies of the R4, assembled in Maubeuge (North), and is preparing to welcome two more new vehicles in 2025: the new Nissan Micra, the tools of which will begin to arrive at the start of the year, then a Mitsubishi vehicle derived from the Scénic. With six electric vehicles and a revamped industrial tool, Renault Douai is ready to relive great years.
The price of energy, even more strategic than the cost of labor?
Regardless of the detractors who believe that producing small electric cars in France is not profitable, Luca de Meo persists and signs. His justification: “The shift to electric vehicles no longer allows labor costs to be used as an excuse.” Josep Maria Recasens, operational director of Ampere, specifies: “The fact that the Renault group decided three years ago to create “Electricity” and to locate the production of all its electric cars in France – in France! not in Romania, Morocco, Spain… in France! – was a strategic decision based on the particularity of the energy available to us in France. Nuclear power plants guarantee direct access to energy with one of the lowest carbon footprints on the planet and at a very competitive price, which more than offsets the cost disadvantages experienced by France.” Josep Maria Recasens estimates that for every euro spent on labor costs, three are spent on energy, recalling in passing that producing an electric vehicle consumes twice as much electricity as for a thermal equivalent, over the entire value chain.